- Grounding, Bonding, and Shielding for Electronic Equipments and Facilities
- Grounding, Bonding, and Shielding for Electronic Equipments and Facilities -Cont.
- Preface
- Table of Contents
- Table of Contents -Cont.
- Table of Contents -Cont.
- Table of Contents -Cont.
- Table of Contents -Cont.
- Table of Contents -Cont.
- Table of Contents -Cont.
- Table of Contents -Cont.
- Table of Contents -Cont.
- List of Figures
- List of Figures -Cont.
- List of Figures -Cont.
- List of Figures -Cont.
- List of Figures -Cont.
- List of Tables
- Chapter 1. New Facilities Design Criteria
- Determination of Site Parameters (Site Survey)
- Figure 1-1. Measurement of Soil Resistivity
- Figure 1-2. Resistivity Determination of a Small Site
- Geological Effects
- Design Procedure
- Landscape features
- Table 1-1 Relative Advantages and Disadvantages of the Principal Types of Earth Electrodes
- Calculation of Earth Resistance
- Figure l-3. Minimum Earth Electrode Subsystem Configuration for Rectangular Shaped Facility
- Figure 1-4. Nomograph for Determining the Resistance to Earth of a Single Ground Rod (1-1)
- Figure 1-5. Effective Resistance of Ground Rods When Arranged in a Straight Line or a Large Circle
- Figure 1-6. Graph of Multiple-Rod Resistance Ratio (1-2)
- Design Guidelines
- Design Guidelines -Cont.
- Figure 1-7. Electrode Configuration for Irregular Shaped Facility
- Figure l-9. Electrode Configuration for Closely Spaced Structures
- Figure 1-10. Grounding System for Typical Radar Installation
- Figure 1-11. Details of Ground Rod/Earth Electrode Subsystem Installation
- Figure 1-13. Typical Grounding Well Installation
- Figure 1-14. Connections to Earth Electrode Subsystem
- Installation Practices
- Principles of Protection
- Size and Materials
- Figure 1-15. Grounding Practices for Lightning Protection
- Figure 1-16. Location of Air Terminals for Common Roof Types
- Figure 1-17. Location of Air Terminals on Gently Sloping Roofs
- Location
- Figure 1-18. Air Terminal Placement on Flat-Roofed Structures
- Figure 1-19. Graphical Method for Determining Need for Additional Air Terminals
- Figure l-20. Field Expedient Technique for Determining the Protection of Prominent Dormers
- Figure 1-21. Illustration of Method for Determining the Protection of Flat Surfaces as Provided by Air Terminals (l-4)
- Grounding Conductors
- Table 1-2 Minimum Requirements for Roof and Down Conductors on Structures Not Greater than 75 Feet (23 Meters) in Height (1-3)
- Table 1-4. Solid Copper Wire - Weight, Breaking Strength, DC Resistance
- Table 1-4. Solid Copper Wire - Weight, Breaking Strength, DC Resistance -Cont.
- Down Conductors
- Figure 1-23. Recommended Construction Practices for Integral Lightning Protection Systems
- Fasteners
- Figure 1-24. The Protected gone Provided by Two Vertical Masts
- Overhead Ground Wire Type
- Waveguide Installation and Grounding
- Figure 1-26. Waveguide Entry Plate Detail
- Figure 1-27. Grounding Detail for Elliptical Waveguide
- Figure 1-28A. Grounding Details for Elliptical Waveguide
- Figure 1-30. Strap Cutting Detail for Elliptical Waveguide
- Figure 1-31. Typical Communication Cable Entry Installation
- Figure 1-33. Grounding Steps for Cables
- Cable Installation and Grounding
- Minimizing Damage
- Frequency of Transient Occurrence
- Induced transient amplitude
- Figure 1-34. Mean Number of Thunderstorm Days Per Year for the United States
- Table 1-6 Parameter for Direct Lightning Strike Current
- Table 1-7. Peak Currents from Direct Lightning Strikes
- Methods for Transient Protection on AC Service Conductors
- Protection of Underground Cables
- Figure 1-35. Lightning Protection for Underground Cables
- Secondary AC Surge Arrester
- Operating Characteristics of Surge Arresters
- Figure 1-36. Secondary AC Surge Arrester Installation, Grounded Service (Single Building from Single Source)
- Figure 1-37. Secondary AC Surge Arrester Installation, Ungrounded Service
- Table 1-10. Transient Occurrences, Low-Incident Lightning Areas
- Important turn-on time characteristics
- Table 1-11. Generalized Characteristics for Surge Arresters by Type
- Reverse standoff voltage
- Desirable Operating Characteristics for Transient Suppressors
- Table 1-12. Typical Maximum Clamp Voltage for Spark Gap Arresters
- Figure 1-38. Typical Operating Curve for Two Series of Gas-Filled Spark Gap Arresters with Nonlinear Series Resistor
- Table 1-14. High Energy ZNR Surge Arrester Typical Characteristics
- Table 1-15. Test Results for Parallel-Connected ZNR
- Hybrid type arresters
- Transient Protection for Externally Exposed Equipment Lines
- Equipment Withstand Levels
- Transient Suppression
- Figure l-40. Typical Transient Suppressor Installation, Facility and Equipment Level
- Operating Characteristics of Transient Suppressors
- Coaxial Cable Shield Connection Through an Entrance Plate
- Transient Suppression for RF Coaxial Line
- Transient Protection
- Transient Definition
- Determination of Equipment Damage (Withstand) Levels
- Determination of Need for Transient Protection
- AC Power Input
- Components
- Figure 1-41. Typical Configuration for Protection of Equipment From Conducted Powerline Surges and Transients (Neutral Grounded)
- Figure 1-42. Typical Configuration for Protection of Equipment from Conducted Powerline Surges and Transients (Ungrounded)
- Functional characteristics
- Landline Transient Suppression
- Control, status, intrafacility power, and audio landlines
- Control, status, intrafacility power, and audio landlines -Cont.
- Figure 1-43. Typical Configuration for Protection of Equipment from Conducted Landline Transients
- Grounding for suppression components/circuits
- Transient suppression for lines in metal conduit
- Figure 1-44. Transient Suppression for Coaxial Lines (DC To 3 MHz)
- Figure 1-45. Transient Suppression for Twinaxial Lines (DC To 3 MHz)
- RF coaxial lines (above 3 MHz)
- Corrosion Control
- Physical Protection
- Configuration of the Equipment Fault Protection Subsystem
- Figure 1-46. Typical Equipment Fault Protection Subsystem
- Pipes and Tubes
- Cable Trays
- Power Distribution Systems
- MIL-STD-188-124A and NEC Compliance Inspection
- Separately derived power sources
- Table 1-20. Grounding Electrode Conductor Size
- Power transfer and bypass switches
- Wireways, raceways, cable trays
- Table 1-21. Equipment Grounding Conductor Size Requirement
- Correction of Deficiencies
- Figure 1-47. Method for Determining the Existence of Improper Neutral Ground Connections
- Higher Frequency Network
- Figure 1-49. Typical Equipotential Ground Plane for Multi-Deck Building
- Figure 1-50. Typical Building Floor Plan (Top View)
- Figure 1-51. Typical Multi-Deck Building Plan (Side View)
- Multipoint Ground System
- Table 1-22 Size of Equipment Ground Cables
- Copper Grid Embedded in Concrete
- Figure 1-52. Elements of the Facility Ground System (with Grid)
- Raised (Computer) Flooring
- Figure 1-54. Ground Connector for Equipotential Plane in Concrete
- Figure 1-56. Examples of Cable to Bar Ground Connectors
- Bolted-Grid (Stringer) or Rigid Grid System Raised Floors
- Figure 1-58.Rigid Grid Floor System Details
- Figure 1-59. Example of Rigid-Grid to Pedestal Bolted Connection
- Figure l-60. Example of Rigid-Grid to Pedestal Clamped Connection
- Figure 1-61. Example of Unacceptable Grid-to-Pedestal Bonding
- Equipment Cabinet Grounding
- Figure 1-63. Example of Pedestal-Only Floor Construction
- Figure 1-64. Typical Equipment Cabinet Grounding Detail
- Grounding Philosophy for Equipments Processing National Security Related Information (Red/Black Equipments)
- Figure 1-65. Typical RED/BLACK Signal Reference Subsystem (High Level Signals)
- Figure 1-66. Typical Red Signal, Shield Ground, Bus Distribution System
- Figure 1-67. Typical Intermediate Distribution Frame (Shield Ground Bus in Distribution Frames)
- Figure 1-68. Typical Intermediate Distribution Frame (Data Concentrator Frame Installation)
- Figure l-69. Facility Power and AC Ground Distribution
- Application Guidelines
- Table 1-23 Minimum Torque Requirements for Bolted Bonds
- Figure l-70. Order of Assembly for Bolted Connection
- Bond Protection Code
- Table 1-25 Bond Protection Requirements
- Table 1-26 Protective Finishes for Bond Members
- Table 1-26 Protective Finishes for Bond Members -Cont.
- Jumper Fasteners
- Figure 1-72. Bonding of Equipment Cabinets to Cable Tray
- Tubing and Conduit
- Figure 1-75. Connection of Bonding Jumpers to Flat Surface
- Figure l-76. Bolted Bond Between Flat Bars
- Figure 1-78. Use of Bonding Straps for Structural Steel Interconnections
- Figure 1-80. Connection of Earth Electrode Riser to Structural Column
- Establishing Requirements
- Figure 1-82. Measured Electromagnetic Shielding Effectiveness of a Typical Building at 45 Feet Inside Outer Wall (1-12)
- Figure 1-83. Shielding Effectiveness of Rebars (1-13)
- Table 1-28 Attenuation Correction Factors for Reinforcing Steel (1-14)
- Figure 1-84. Shielding Effectiveness of a Grid as a Function of Wire Diameter, Wire Spacing, and Wavelength (1-15)
- Design Guidelines
- Selection of Materials
- Figure 1-85. Shield Absorption Loss Nomograph (1-17)
- Construction Guidelines
- Table 1-29 Relative Conductivity and Relative Permeability of Common Metals
- Table 1-29 Relative Conductivity and Relative Permeability of Common Metals -Cont.
- Figure 1-86. Nomograph for Determining Magnetic Field Reflection Loss (1-17)
- Figure l-87. Nomograph for Determining Electric Field Reflection Loss (1-17)
- Figure l-88. Nomograph for Determining Plane Wave Reflection Loss (1-17)
- Figure l-90. Shielding Effectiveness of Copper Foil Shielded Room (1-18)
- Figure l-92. Good Corner Seam Design
- Figure 1-93. Pressure Drop Though Various Materials Used to Shield Ventilation Openings
- Design Practices
- Instrumentation Considerations
- EMP Shield Applications
- Figure l-94. Typical Single-Point Entry for Exterior Penetrations (Top View)
- Figure l-95. Entry Plate Showing Rigid Cable, Conduit, and Pipe Penetrations
- Construction Guidelines
- General Tactical Grounding Requirements
- Soil Resistance
- Table l-30. Soil Resistivity (ohm-m)
- Figure 1-96. Effect of Rod Length on Ground Resistance
- Figure 1-97. Grounding of 120/20 V 3-Phase,4-Wire Wye Power Distribution System
- Terminal Protection Devices
- Figure l-98. Grounding of Single-Phase, 3-Wire 110/220V Power System
- Figure l-99. Grounding of 28V DC P-Wire DC Power System
- Detailed Tactical Grounding Requirements
- Training
- Stand-Alone Shelter
- Collocated Shelters
- Figure l-100. Connecting Ground Subsystems for Collocated Shelters Greater than 20 Feet Apart
- Fixed Prefabricated Shelters
- Fences
- Figure l-101. Method of Grounding a Fence
- Earth Electrode Subsystem
- Lightning Protection Network
- Bonds and Bonding
- Earth Electrode Subsystem
- Lighting Protection Network
- Lighting Protection Network -Cont.
- Bonding
- References
- References -Cont.
- Chapter 2 Existing Facilities
- Figure 2-1. Transmitter Building
- Figure 2-2. Communication Center/Receiver Building Expansion
- Facility Survey
- Earth Electrode Subsystem
- Earth Electrode Subsystem -Cont.
- Figure 2-3. Earth Resistance Measurement at a Typical Facility
- Figure 2-4. Resistance Measurement Work Sheet
- Figure 2-5. Sample of a Completed Resistance Measurement Work Sheet
- Bonds and Bonding
- Figure 2-6. Typical Bonding Deficiencies
- Figure 2-7. Typical Bonding Deficiencies
- Lightning Protection Network
- Figure 2-8. Severely Damaged Down Conductor
- Figure 2-9. Method for Determining the Existence of Improper Neutral Ground Connections
- Safety Grounding
- Signal Grounding Practices
- Figure 2-11. Typical Bond Resistance and Stray Current Measurement Locations in an Electronic Facility
- Shielding
- Ground System Noise Current
- Figure 2-12. Bond Resistance Measurement Technique
- Differential Noise Voltage
- Figure 2-14. Oscilloscope Connections for Measuring Voltage Levels on Ground Systems
- Earth Electrode Subsystem
- Earth Electrode Subsystem -Cont.
- Bonds
- Lighting Protection Subsystem
- Lighting Protection Subsystem -Cont.
- Fault Protection Subsystem
- Fault Protection Subsystem -Cont.
- Signal Reference Subsystem Grounding
- Noise and Current Levels
- Guidelines for Upgrading
- Guidelines for Upgrading -Cont.
- Expansion of Existing Facilities
- Schedules and Records
- Figure 2-15. Example of Equipotential or Multipoint Grounding
- Figure 2-16. Major Discrepancy Report Form
- Facility Maintenance Procedure (Earth Electrode Subsystem).
- Procedure
- Facility Maintenance Procedure (Lightning Protection Subsystem)
- Facility Maintenance Procedure (Bonding)
- Facility Maintenance Procedure (Fault Protection Subsystem (Safety Ground)
- Facility Maintenance Procedure (Signal Reference Subsystem (Signal Grounding)
- Facility Maintenance Procedure (Shielding)
- Facility Maintenance Report
- Inspection Checklist
- Lighting Protection Subsystem
- Inspection Checklist
- Bonding
- Fault Protection Subsystem (Safety Ground)
- Signal Reference Subsystem Grounding
- Facility Shielding (Designated IF Barrier)
- Performance Evaluation Program
- Performance Evaluation Program Grounding ,Bonding, Shielding
- Performance Evaluation Program Grounding ,Bonding, Shielding -Cont.
- Performance Evaluation Program Grounding ,Bonding, Shielding -Cont.
- Performance Evaluation Program Grounding ,Bonding, Shielding -Cont.
- Existing Facilities
- Signal Reference Subsystem
- Grounding Precautions
- Figure 2-17. Typical Multiple Area Ground Distribution (OLD RED/BLACK CRITERIA)
- Figure 2-18. Typical Signal, Shield Ground, Bus Distribution System for Single-Point Ground (OLD RED/BLACK CRITERIA)
- Figure 2-19. Crypto Equipment Grounds (OLD RED/BLACK CRITERIA)
- Figure 2-20. Typical Facility Ground System (OLD RED/BLACK CRITERIA)
- Chapter 3 Design Criteria
- Lower Frequency Equipment
- Figure 3-1. Grounding in Lower Frequency Equipment
- Signal Interfacing
- Figure 3-2. Lower Frequency Signal Ground Bus Bar Installation in Rack or Cabinet
- Shield Grounding (Black Only)
- Figure 3-3. Use of Balanced Lines to Avoid Ground Loops
- Figure 3-4. Effect of an Unbalanced Cable on the Single-Point Ground
- Figure 3-5. Effect of Arbitrarily Grounding the Source End of Unbalanced Equipment Interconnecting Cables
- Figure 3-6. Method of Grounding the Individual Shields on Long Lower Frequency Shield Cables
- Figure 3-7. Grounding of Overall Cable Shields to Connectors
- Higher Frequency Equipment
- Signal Interfaces
- Equipments Containing Both Lower and Higher Frequency Circuits
- Figure 3-10. Grounding Practices in Equipments Containing Both Higher Frequency and Lower Frequency Circuits
- Cabinet Grounding
- Figure 3-11. Typical Equipment Cabinet Grounding Detail
- Bonding Practices
- Figure 3-12. Acceptable and Unacceptable Uses of Bonding Jumpers
- Bonding Practices -Cont.
- Figure 3-14. Bonding of Equipment to Mounting Surface
- Figure 3-16. Bonding of Rack-Mounted Equipments Employing Dagger Pins
- Figure 3-17 Recommended Practices for Effective Bonding in Cabinets
- Figure 3-19. Bonding of Connector to Mounting Surface
- Shielding Guidelines
- Layout and Construction
- Equipment Enclosures
- Penetrations and Apertures
- Figure 3-21. Mounting of Gasket on Hinged Side of Equipment Doors and Panels
- Table 3-1 Frequency Properties of Standard Sizes of Honeycomb
- Figure 3-22. Illustration of Proper and Improper Shield Penetrations
- Figure 3-23. Use of Cylindrical Waveguide-Below-Cutoff for Control Shaft Shield Penetration
- Figure 3-25. Acceptable Methods of Shielding Panel-Mounted Meters
- Common-Mode Noise Control
- Analog Systems
- Figure 3-27. Grounding Practices for Differential Amplifiers
- Figure 3-28. Method of Grounding Bridge Transducers
- Ungrounded Transducers
- Figure 3-30. Recommended Grounding Practices for Floating Transducers
- Digital Data Systems
- Figure 3-32. Resistive Isolation of Data Channels
- Strip Chart Recorders
- Lower Frequency Equipments
- Lower Frequency Equipments -Cont.
- Figure 3-33. Signal Ground Terminal Isolation Resistance Test for an Individual Equipment
- Figure 3-34. Signal Ground Terminal Isolation Resistance Test for an Equipment Assembly
- Higher Frequency Equipments
- Figure 3-35. Measurement of Connector Bonding Resistance
- Shielding
- Instrumentation System
- Signal Grounding
- Installed Equipments
- Shielding
- Other Observations
- Chapter 4 Notes
- Appendix A Glossary
- Appendix A Glossary -Cont.
- Appendix A Glossary -Cont.
- Appendix A Glossary -Cont.
- Appendix A Glossary -Cont.
- Appendix A Glossary -Cont.
- Appendix B Supplemental Bibliography
- Appendix B Supplemental Bibliography -Cont.
- Appendix B Supplemental Bibliography -Cont.
- Appendix B Supplemental Bibliography -Cont.
- Appendix B Supplemental Bibliography -Cont.
- Appendix B Supplemental Bibliography -Cont.
- Appendix B Supplemental Bibliography -Cont.
- Appendix B Supplemental Bibliography -Cont.
- Appendix B Supplemental Bibliography -Cont.
- Appendix B Supplemental Bibliography -Cont.
- Appendix B Supplemental Bibliography -Cont.
- Appendix B Supplemental Bibliography -Cont.
- Appendix B Supplemental Bibliography -Cont.
- Appendix B Supplemental Bibliography -Cont.
- Appendix B Supplemental Bibliography -Cont.
- Appendix B Supplemental Bibliography -Cont.
- Appendix C Table of Contents for Volume I
- Appendix C Table of Contents for Volume I -Cont.
- Appendix C Table of Contents for Volume I -Cont.
- Appendix C Table of Contents for Volume I -Cont.
- Appendix C Table of Contents for Volume I -Cont.
- Appendix C Table of Contents for Volume I -Cont.
- Appendix C Table of Contents for Volume I -Cont.
- Appendix C Table of Contents for Volume I -Cont.
- Appendix C Table of Contents for Volume I -Cont.
- Appendix D Index
- Appendix D Index -Cont.
- Appendix D Index -Cont.
- Appendix D Index -Cont.
- Appendix D Index -Cont.
- Appendix D Index -Cont.
- Appendix D Index -Cont.
- Appendix D Index -Cont.
- Appendix D Index -Cont.
- Appendix D Index -Cont.
- Appendix D Index -Cont.
- Appendix D Index -Cont.
- Appendix D Index -Cont.
- Appendix D Index -Cont.
- Appendix D Index -Cont.
- Appendix D Index -Cont.
- Appendix D Index -Cont.
- Appendix D Index -Cont.
- Appendix D Index -Cont.
- Appendix D Index -Cont.
- Appendix D Index -Cont.
- Appendix D Index -Cont.
- Appendix D Index -Cont.
- Appendix D Index -Cont.
- Blank Page
- Blank Page
Grounding, Bonding, and Shielding for Electronic Equipments and Facilities
|
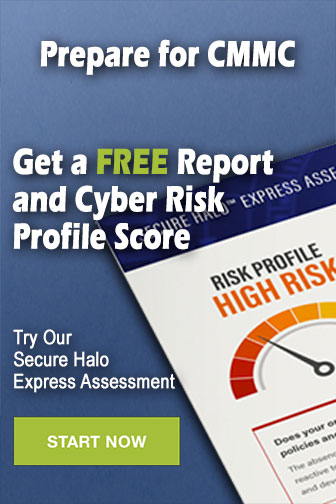
|